Designing Trays for Automated Denesting
Many products, from plastic cups to ice cream cones, are stacked in a nested configuration to minimize the amount of space needed to store them. “Denesting” is the process of separating items that are stacked together.
In manufacturing operations that place product in trays, production and filling rates can only be increased as quickly as trays can be separated and placed onto the line. Because of this, manufacturers are turning to automated denesting equipment to increase efficiency and profitability.
While the trays themselves may be an inexpensive piece of the finished product, improper design or tray dispensing issues can be costly. Trays need to be placed on line in the proper position, every time, in order to avoid spilling product or disrupting processes further down the line.
To get the most accurate tray placement at the highest rate, there are several design elements you should consider when designing a tray for use with automated denesting equipment. MGS is not a manufacturer of trays, but we have seen quite a few different tray designs in the 40 years we’ve been building product handling equipment. The knowledge and experience we have gained by handling a wide variety of trays has given us some insight into designing trays for automation.
If your production line deploys a wide variety of tray designs, vacuum pick and place technology offers the most flexibility for tray denesting. There are three types of picking motion utilized by pick and place machines: standard reciprocating motion, straight-line motion and sidewall denest motion. You should consider what type of picking motion is being employed when designing your trays.
One tray design element that would change based on the type of pick motion used is the smooth, flat areas designed for vacuum cup contact. Typically these areas are approx. 1½” in diameter and strategically located on a tray bottom or wall so that a vacuum cup can seat without leaking.
Standard Reciprocating Motion
Due to the motion of the standard reciprocating machines, the pick point for most trays is toward the bottom edge of the tray. Placing flat spots along the bottom edge ensures the most successful vacuum cupseal.
Straight-Line Motion
Straight-line motion machines are quite flexible and compatible with a variety of tray styles. This picking motion pulls the entire tray, as uniformly as possible, straight out of the magazine. Because of this, the denester requires an additional vacuum apparatus. Flat spots should be located as close as possible to each corner of the tray to ensure a good vacuum cup seal and to avoid tray damage.
Sidewall Denesting Motion
This motion is used when tray material is very thin or no flat spot is provided along the bottom of the tray. Tray walls must be flat, smooth, and at least 1” tall in order to ensure good vacuum cup seal.
DENESTING LUGS
Denesting lugs are additional features that enable automated tray feeding. Lugs allow for separation of trays when stacked and permits the insertion of a hold back clip between trays when needed.
Typical / Alternating Lugs
The typical denesting lug is designed so that the lugs of one tray sit on top of the flange of the next tray. Design of each lug is the same, but consecutive trays in a stack cannot have the same lug location. This requires traysto be manufactured on a multiple head die and collated in sequence so the lugs do not line up.
Reverse Lugs
Similar to standard lugs, the reverse lug is also designed so that the lugs of one tray sit on top of the flange of the next tray. A benefit of a reverse lug is that the tray can be made on a single-up mold. Since each tray is the same, no collation sequence is required. However, these lugs are more difficult to produce because they are created by notching the mold in an opposite draft from the rest of the tray. This can make the release from the mold during forming very difficult. Designing a reverse lug so that it is effective can be tricky due to the constant struggle between production concerns and packaging concerns. If the lug is too large, tray production and output can suffer. If the lug is too small, it will not accomplish its task to keep the trays separated so that they can be automatically denested.
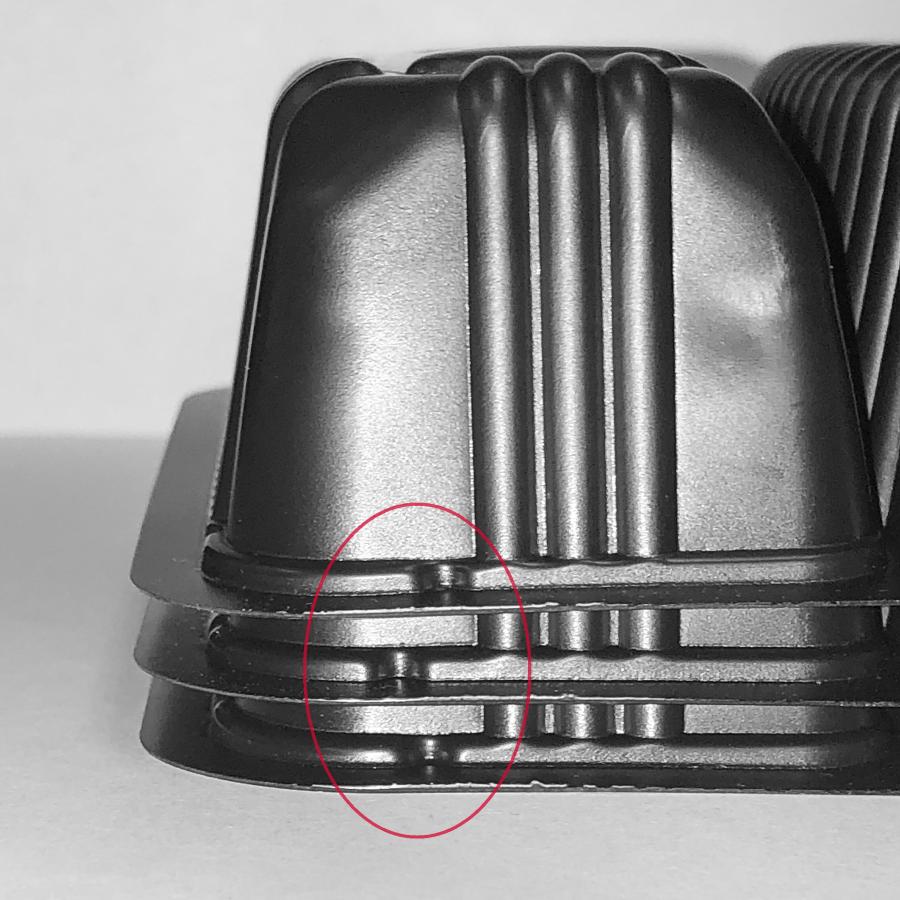
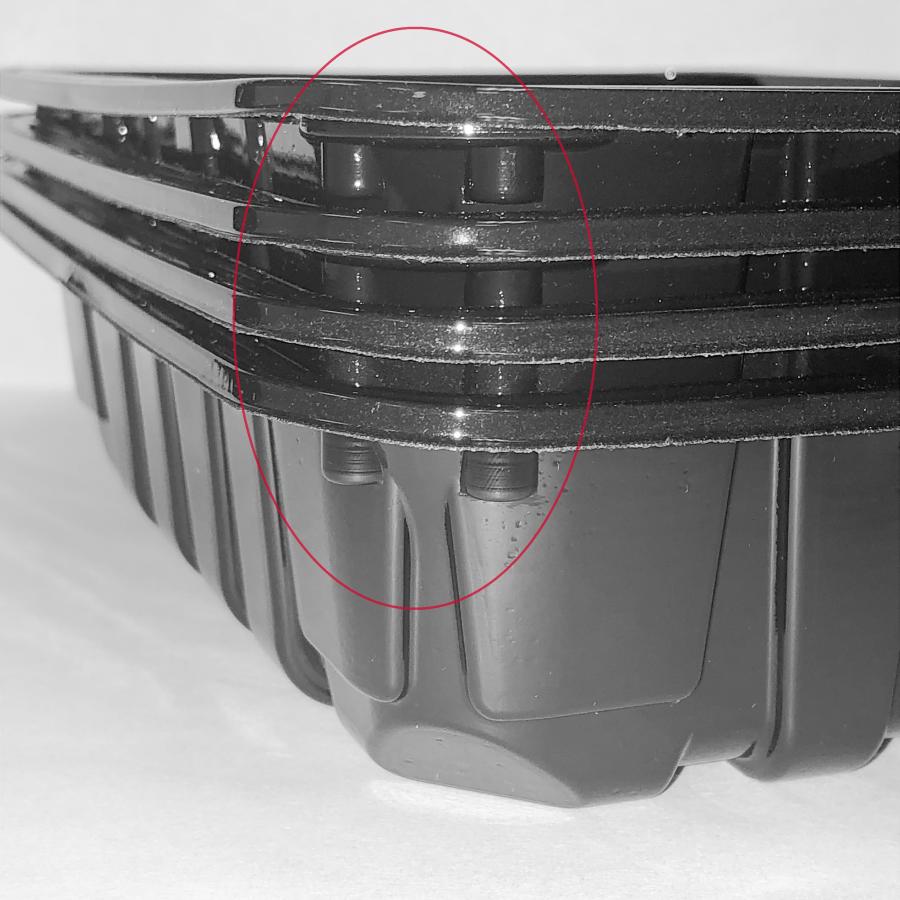
It is our goal to be a valuable resource and partner. If you have any questions on tray design for automated denesting, feel free to reach out to us at info@mgsmachine.com